How To Solve The Burr Of Aluminum Castings
The burr phenomenon of aluminum alloy is inevitable, and there are many methods to deal with the burr. In the production process of die casting, due to factors such as pressure shock and insufficient clamping force, burrs are inevitable. In recent years, with the increasing quality requirements of die castings, the requirements for burrs have become more stringent, and methods of deburring have also emerged endlessly.
The deburring process is the most annoying. china aluminum decoration base manufacturer introduces you to various aluminum casting solutions, which can help you better understand the various deburring methods. And according to your needs to choose the appropriate deburring method.
1. Artificial deburring
This is the most traditional and commonly used method in die-casting plants, using files (files include manual files and pneumatic files), sandpaper, belt machines, grinding heads, etc. as auxiliary tools.
Disadvantages: labor cost is expensive, efficiency is not very high, and it is difficult to remove complex cross holes.
Applicable object: aluminum casting foundry with low technical requirements for workers, small burr and simple product structure.
2.Die deburring
Deburring is performed by using a production die and a punch.
Disadvantages: Requires a certain die (rough die + fine die) production cost, and may also need to make a shaping die.
Applicable object: It is suitable for aluminum alloy die-casting parts with relatively simple parting surface, which has better efficiency and deburring effect than artificial.
3.Grinding and deburring
This type of deburring includes vibration, sand blasting, and rollers, which are currently used in die casting plants.
Disadvantages: There is a problem that the removal is not very clean. It may require subsequent manual treatment of residual burrs or deburring with other methods.
Applicable object: Suitable for small aluminum alloy die-castings with larger batches.
4, frozen deburring
The burrs are rapidly brittled by cooling down, and then the blasts are ejected to remove the burrs. The price of the equipment is about two to three hundred thousand;
Applicable object: Suitable for aluminum alloy die-casting with smaller burr wall thickness and smaller volume.
5, hot deburring
Also called thermal deburring, explosion deburring. By passing some easy gas into an equipment furnace, and then using some media and conditions to make the gas explode instantly, use the energy generated by the explosion to dissolve and remove burrs.
Disadvantages: expensive equipment (prices of millions), high operating technology requirements, low efficiency, and side effects (rust, deformation);
Applicable object: mainly used in some high-precision parts and components, such as automotive and aerospace and other precision parts.
6.Deburring of engraving machine
The equipment price is not very expensive (tens of thousands).
Applicable object: It is suitable for simple space structure and simple and regular deburring positions.
7. Chemical deburring
Using the principle of electrochemical reaction, deburring is automatically and selectively performed on parts made of metallic materials.
Applicable object: Suitable for internal burrs that are difficult to remove, suitable for small burrs (thickness less than 7 wires) of pumps, valves and other products.
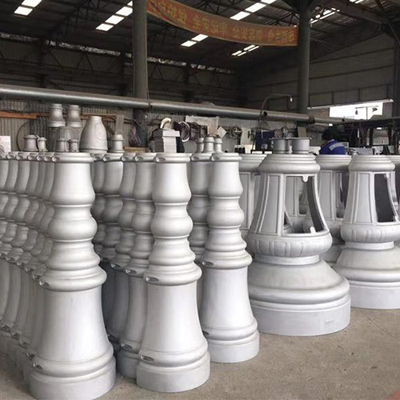
Aluminum Casting Foundry
评论
发表评论