【Aluminum Casting supplier】Advantages and disadvantages of die casting manufacturing
Advantages and disadvantages of die casting manufacturing
Die casting - Die-Casting Tooling Design is a kind of precision casting method that USES high pressure to force the metal into the complex shape of metal mold. In 1964, the Japanese Die Casting association defined Die Casting as "a Casting method in which molten alloy is pressed into precision Casting mould at high temperature and high precision and fine Casting surface are produced in large quantities in a short time ". It is called Die Casting in America and Pressure Die Casting in Britain. The castings made by Die casting are called Die castings.
The tensile strength of these materials is nearly twice as high as that of ordinary cast alloy, which has more positive significance for aluminum alloy automobile wheel hub, frame and other parts that hope to be produced with higher strength impact resistant materials.
The advantages of die casting include excellent dimensional accuracy. This usually depends on the casting material, with a typical value of 0.1mm off the original 2.5cm size and 0.002mm off for every 1cm increase. Compared with other casting processes, the casting surface is smooth and the radius of rounded corners is about 1-2.5 microns. Castings with wall thickness of about 0.75mm can be made as opposed to sandbox or permanent casting. It can be used to directly cast internal structures, such as silk sleeves, heating elements, and high-strength bearing surfaces. Other advantages include the ability to reduce or avoid secondary machining, fast production, casting tensile strength of up to 415 mpa, and the ability to cast highly liquid metals.
The biggest disadvantage of die casting is the high cost. Casting equipment and moulds and mould-related components are expensive compared to other casting methods. Therefore, it is economical to produce a large quantity of products when making die castings. Other drawbacks include that the process is only suitable for highly mobile metals and that the casting quality must be between 30g and 10kg. [5] in normal die casting, there are always holes in the last castings. As a result, no heat treatment or welding is possible, as the gases in the gaps expand under the heat, leading to micro-defects in the interior and peeling of the surface.
That's all for the sharing, thanks for your reading, and we also supply Aluminum Casting design for sale, if you have any demand for our products, just feel free to contact us.
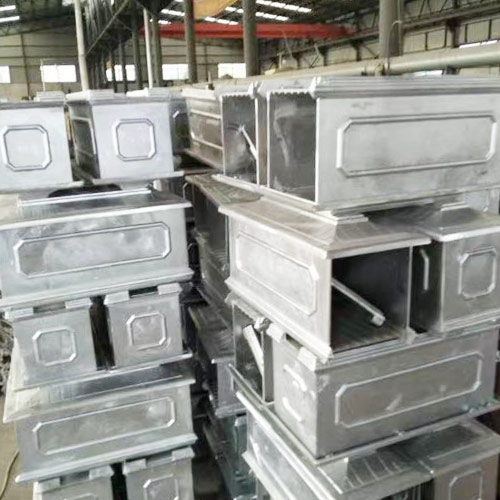
评论
发表评论