The main defect of aluminum alloy casting is crack
The main defect of aluminum alloy casting is crack
1. Casting crack: a crack on the aluminum Casting Foundry formed at a high temperature. It is easy to occur when the casting volume shrinkage is large and the thermal expansion coefficient is large.
2. Heat treatment crack: it often appears as transgranular crack due to excessive heat treatment or overheating.
Causes of cracks: unreasonable Aluminum Casting design, sharp Angle, wall thickness changes too much. In this case, cracks should be improved casting structure design, avoid sharp corners, wall thickness to uniform, smooth transition. Sand mold yield bad will also produce cracks. Measures should be taken to increase sand mold yield. Local overheating of the casting mold will lead to cracks. It is necessary to ensure that all parts of the casting solidify at the same time or in sequence, and improve the design of casting system. Too high casting temperature will produce cracks, so the casting temperature should be appropriately reduced. The thermal correction method should be used to control the cooling time of casting when the casting is taken out too early and will be deformed. Heat treatment overheating, excessive cooling speed after crack, casting deformation using thermal correction method. Control heat treatment temperature correctly, reduce quenching cooling speed.
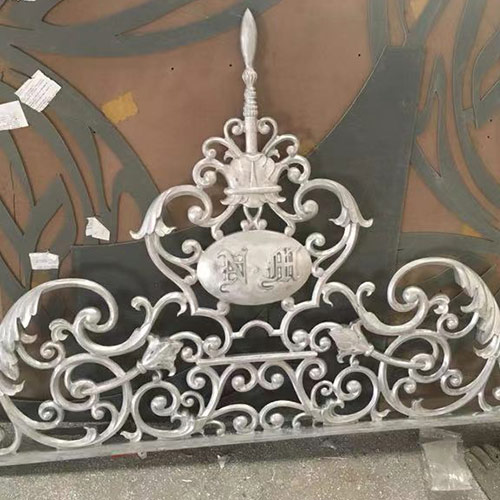
评论
发表评论